Empower your workforce with AI-driven tools for success – transforming safety, efficiency, and downtime reduction on the shopfloor
In the fast-paced world of manufacturing, blue-collar workers on the shopfloor often encounter significant challenges when it comes to troubleshooting machinery, training, and ensuring safety. These obstacles can lead to inefficiencies, increased downtime, and communication barriers.
The Shopfloor AI Assistant leverages cutting-edge AI technology to empower blue-collar workers with real-time, step-by-step troubleshooting guidance. The solution ensures quick, accurate issue resolution and significantly reduces downtime by providing AI-generated first-draft root cause analysis based on asset images. In addition, it features interactive training modules and multilingual safety instructions to enhance communication and safety across diverse workforces.
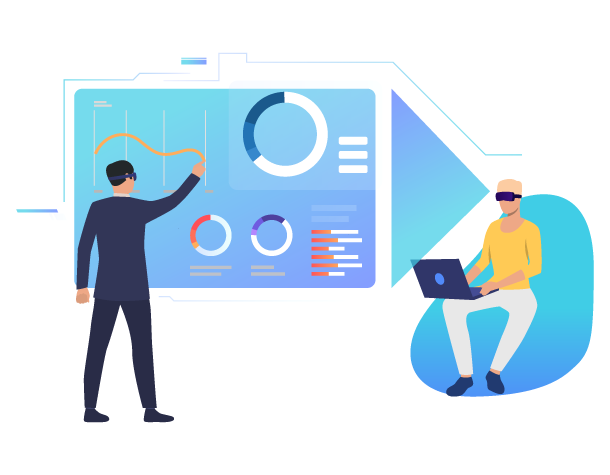
Key Features of the Shopfloor AI Assistant
Receive easy-to-follow, real-time instructions to resolve machinery issues with confidence.
AI-powered RCA generated from asset images to quickly identify the source of problems and expedite resolution.
Interactive training modules that help workers improve their skills and onboard efficiently, ensuring a more knowledgeable workforce.
Contextual safety guidelines integrated directly into workflows, promoting safer working environments.
Multiple language options to ensure clarity and accessibility for workers from diverse linguistic backgrounds.
Voice-enabled support for hands-free operation, allowing workers to focus on tasks while ensuring safety and convenience.
Why Choose the Shopfloor AI Assistant?
Empower your workforce with the tools they need to succeed. The Shopfloor AI Assistant offers a comprehensive, AI-driven solution that reduces complexity, enhances training, and improves safety. Designed for modern manufacturing environments, it ensures that your team stays productive, safe, and efficient.
Impact on Manufacturing Operations
The Shopfloor AI Assistant not only improves the efficiency of day-to-day operations but also enhances overall decision-making, risk management, and compliance. By integrating seamlessly into manufacturing environments, it proactively identifies risks, reduces downtime, and ensures that safety protocols are followed. The solution is designed to drive operational excellence, making it an essential tool for the modern manufacturing workforce.
Enhanced Decision-Making
Timely and accurate insights enable informed decisions, reducing downtime and improving productivity.
Proactive Risk Identification
Ensures compliance with safety standards and identifies potential risks before they become problems.
Seamless Integration
Easily integrates with existing workflows and systems, fostering collaboration across departments.
Increased Efficiency
Reduces downtime, optimizes operations, and increases productivity across the shopfloor
Reduced Operational Costs
Minimizes downtime and inefficiencies, reducing operational costs for a more efficient production process.
Enhanced Worker Safety
AI-powered safety instructions and alerts ensure safety protocols, reducing accidents and improving safety.
Our Clients
Challenges Facing the Shopfloor Workforce
Machinery issues are often complex, and workers lack accessible, easy-to-follow guidance, leading to delays in identifying and resolving problems.
The process of conducting root cause analysis can be slow and inefficient, prolonging downtime and disrupting productivity.
Training and onboarding processes are manual, inconsistent, and time-consuming, creating gaps in skill development.
Safety instructions are often unclear, and language barriers can exacerbate the risk of miscommunication, compromising worker safety and operational efficiency.