If you are considering implementing Dynamics 365 Supply Chain, it is important to work with a qualified implementation partner. A good implementation partner can help you assess your needs, select the right modules and features, and implement the system in a way that meets your specific requirements.
Dynamics 365 Supply Chain is a cloud-based ERP system that helps businesses improve their supply chain operations. It offers a wide range of features, including inventory management, warehouse management, order management, procurement and vendor management, production planning and scheduling, demand planning and forecasting, quality management, compliance and regulatory requirements implementation, customer relationship management (CRM) integration, financial management and accounting integration, service management and field service integration, business intelligence and analytics, IoT (Internet of Things) integration for real-time data monitoring, mobile app development and integration, multi-language and multi-currency support, cloud migration and deployment, and continuous improvement and ongoing support.
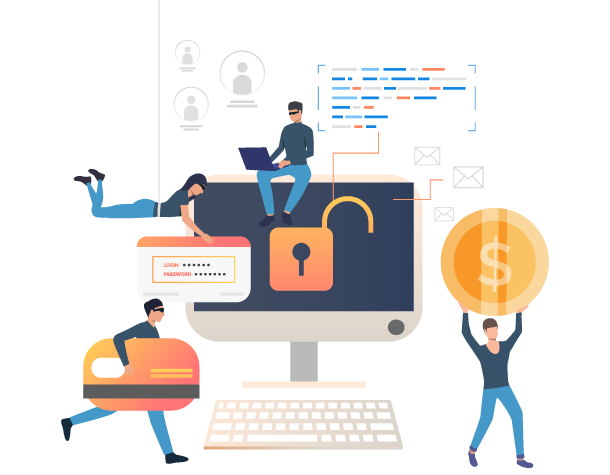
atQor is a Microsoft Gold Partner and a leading provider of IT solutions and services, including implementation and customization of Microsoft Dynamics 365 Supply Chain Management (SCM) ERP systems. With over 20 years of experience in the IT industry, atQor has a proven track record of success in helping businesses of all sizes improve their supply chain operations.
Dynamics 365 SCM is a cloud-based ERP system that helps businesses streamline and optimize their supply chain processes, including inventory management, warehouse operations, and procurement. It offers a wide range of features and capabilities, including:
- Inventory management: Track inventory levels, manage stock orders, and optimize inventory costs.
- Warehouse operations: Manage warehouse space, track inventory movement, and optimize warehouse processes.
- Procurement: Manage supplier relationships, source and purchase materials, and track procurement costs.
- Demand planning: Forecast demand, manage supply chain risks, and optimize production schedules.
- Quality management: Track quality metrics, identify and resolve quality issues, and improve product quality.
- Compliance and regulatory requirements: Ensure compliance with industry regulations and standards.
- Customer relationship management (CRM) integration: Integrate Dynamics 365 SCM with CRM systems to improve customer service and increase sales.
- Financial management and accounting integration: Integrate Dynamics 365 SCM with financial management and accounting systems to improve financial reporting and decision-making.
When engaging atQor for Dynamics 365 SCM implementation, you can expect the following:
- Requirements gathering: atQor consultants will work closely with your organization to understand your business processes, objectives, and specific requirements related to supply chain management.
- Solution design: Based on the gathered requirements, atQor will design a tailored solution using the features and capabilities of Dynamics 365 SCM. This includes configuring modules, defining workflows, and customizing the system to align with your business processes.
- System configuration: atQor will set up and configure the Dynamics 365 SCM system according to the designed solution. This involves configuring master data, defining roles and permissions, and setting up system parameters.
- Data migration: If you have existing data in legacy systems or other sources, atQor will assist in migrating the relevant data into Dynamics 365 SCM. This ensures a smooth transition and continuity of operations.
- System customization: If your organization requires additional functionality or modifications beyond the standard features of Dynamics 365 SCM, atQor can develop customizations or integrations to meet your unique needs.
- User training: atQor will provide comprehensive training sessions to educate your employees on how to use the Dynamics 365 SCM system effectively. This includes training on core functionalities, data entry, reporting, and system administration.
- Testing and quality assurance: Before going live, the implemented system will undergo rigorous testing to ensure its stability, accuracy, and compliance with your requirements. atQor will perform functional and integration testing and resolve any issues identified.
- Deployment and go-live: Once the system has been thoroughly tested and approved, atQor will assist in deploying the solution to your production environment. This involves data validation, final configurations, and transitioning users from the old system to Dynamics 365 SCM.
- Post-implementation support: atQor provides ongoing support and maintenance services to address any issues, perform system updates, and assist with user inquiries or system enhancements.
By partnering with atQor , you can be confident that your Dynamics 365 SCM implementation will be successful. We have the experience, expertise, and resources to help you achieve your supply chain goals. Contact us today to learn more about our Dynamics 365 SCM implementation services.
Ongoing Support and Maintenance for Dynamics 365 Supply Chain ERP
Establish a relationship with the Dynamics 365 vendor or an authorized partner who can provide technical support and guidance. They can assist with troubleshooting, bug fixes, and updates related to the ERP system.
Set up a help desk or ticketing system to centralize user requests and issue reporting. This allows for efficient tracking, prioritization, and resolution of problems encountered by end-users.
Provide ongoing training and documentation for end-users to ensure they have the necessary skills to utilize the ERP system effectively. This can include regular training sessions, user manuals, online resources, and FAQs.
Implement monitoring tools to keep track of system performance, identify bottlenecks, and proactively address any issues. Regular system health checks, database maintenance, and performance tuning can help optimize the ERP system's performance.
Regularly review and update user access permissions to ensure data security. Implement security best practices, such as role-based access controls, strong passwords, and data encryption, to protect sensitive information.
Stay up to date with the latest Dynamics 365 Supply Chain updates and releases. Evaluate the impact of new features and bug fixes, and plan and test system upgrades to ensure a smooth transition to newer versions.
Ongoing support and maintenance are crucial aspects of any ERP implementation, including Dynamics 365 Supply Chain. Once the initial implementation is completed, it's essential to have a plan in place to ensure the system's continuous operation, updates, and addressing any issues that may arise.
Services
Business process analysis and requirement gathering
System design and architecture planning
Data migration and integration
Customization and configuration of Dynamics 365 Supply Chain
User training and change management
Project management and implementation planning
Testing and quality assurance
Go-live support and post-implementation maintenance
User acceptance testing (UAT) coordination
Workflow and process automation
Report and dashboard development
Master data management
Supply chain planning and forecasting
Inventory management
Warehouse management
Order management
Procurement and vendor management
Production planning and scheduling
Demand planning and forecasting
Quality management
Compliance and regulatory requirements implementation
Customer relationship management (CRM) integration
Financial management and accounting integration
Service management and field service integration
Why Choose atQor for Dynamics 365 Supply Chain ERP Implementation?
atQor is a leading Microsoft Partner with extensive experience in implementing Dynamics 365 Supply Chain ERP. We offer a comprehensive range of services, from consultation and planning to deployment and ongoing support.
Our Expertise
Our team of experts has a deep understanding of Dynamics 365 Supply Chain ERP and the unique requirements of different industries. We have successfully implemented Dynamics 365 Supply Chain ERP for a wide range of businesses, including manufacturing, distribution, retail, and healthcare.
Planning and Analyzing a Dynamics 365 Supply Chain ERP Implementation
Planning and implementing an ERP (Enterprise Resource Planning) system, such as Dynamics 365 Supply Chain, can be a complex process. To ensure a successful implementation, it is crucial to follow a structured approach. Here is a step-by-step guide for planning and analyzing a Dynamics 365 Supply Chain ERP implementation:
Define objectives and scope.
Clearly identify the goals and objectives of implementing Dynamics 365 Supply Chain ERP. Determine the scope of the implementation, including the modules and functionalities you plan to use.
Assemble a project team.
Form a cross-functional team comprising individuals from various departments, such as IT, operations, finance, and supply chain. Assign a project manager to oversee the implementation process.
Conduct a current state analysis.
Evaluate your existing processes, systems, and data flows. Identify pain points, inefficiencies, and areas that need improvement. This analysis will serve as a baseline for designing the future state with Dynamics 365 Supply Chain.
Develop a project plan.
Create a detailed project plan that includes tasks, milestones, timelines, and resource allocation. Define key deliverables and establish a realistic timeline for each phase of the implementation.
Perform a gap analysis.
Compare the current state with the desired future state to identify the gaps that need to be addressed. Determine how Dynamics 365 Supply Chain can help you close these gaps.
Communicate with stakeholders.
Keep all stakeholders informed of the project's progress, challenges, and opportunities. This will help to ensure that everyone is on the same page and that the project stays on track.
Solution Design:
Once the requirements have been gathered, the next step is to design a solution. This involves defining the overall solution architecture, considering factors such as scalability, security, and performance.
Our Clients
Deployment and Go-Live of a Dynamics 365 Supply Chain ERP Implementation
The first step is to configure the Dynamics 365 Supply Chain ERP system based on the organization's specific requirements. This includes setting up modules, defining workflows, creating user roles, and configuring any customizations or integrations.
The next step is to migrate data from the organization's legacy systems or existing ERP into Dynamics 365. This involves extracting data, transforming it to fit the new system's format, and loading it into the ERP. It is important to validate the data during this process to ensure accuracy.
Once the data migration is complete, integration testing should be conducted. This involves testing the interfaces and integrations between Dynamics 365 and other systems to ensure seamless data flow and functionality.
UAT is performed by end users to validate the system's functionality and ensure it meets their specific business requirements. Test scenarios are executed, and any issues or gaps are identified and resolved before moving forward.
User training is crucial to ensure successful adoption of the new system. Conduct training sessions for employees who will be using Dynamics 365, covering modules, processes, and any changes in workflows. Training can be conducted through workshops, documentation, or online resources.
In some cases, organizations opt for a parallel run phase where the old system and the new Dynamics 365 system run simultaneously for a period of time. This allows users to compare the outputs and identify any discrepancies or issues before fully transitioning to the new system.
Before go-live, the entire system should be thoroughly validated to ensure all configurations, integrations, and customizations are working correctly. Perform end-to-end testing to validate the system's stability, data accuracy, and performance.
A detailed go-live plan should be developed, outlining the specific tasks, responsibilities, and timelines for the actual go-live event. It should include considerations for system downtime, user support, and contingency plans in case of any issues during the transition.
On the designated go-live date, the new Dynamics 365 Supply Chain ERP system is made live for use by the organization. This involves switching off the old system and enabling access to the new system for all users. It is important to have a support team available to address any immediate concerns or issues that may arise.
After go-live, provide ongoing support to users as they transition to the new system. Monitor system performance, address user queries and issues, and ensure any necessary adjustments or refinements are made.